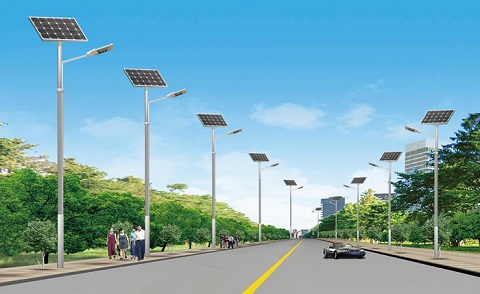
The street lights help to keep our roads safe at the evening and are way out of reach, but every time we drive past them with never a thought of their manufacture. They are a worldwide feature located on all important roads and are often
manufactured from custom aluminum.
Street lights made from custom aluminum -- it's an obvious choice, due not just to the ease of manufacture but also to the native qualities of aluminum.
The street light columns must have the following qualities:
light weight
durable
good quality
safety
high corrosion resistance
inexpensive of maintenance
In an industry connected with continuous innovation and revamping, the versatility of custom aluminum not only increases the efficiency in manufacturing and setting up various components, but offers an option that is both aesthetically
pleasing and functional.
Street Lights can be made from steel or aluminum. However extruded aluminum allows for elegant, low maintenance columns with green credentials and increased design innovation possibilities.
Aluminum light columns are produced using a very different procedure to that of steel columns. The extrusion processing enables an array of cross sections and curves and that can be incorporated into the column design and manufacturing
process.
Surface Treatment
Aluminum column surface finishing can be anodized, painted or powder coated to provide color variations and extra weather protection.
As road safety demands are continually refined it is necessary not only to meet but exceed those requirements. extruding aluminum columns and fittings offer a lightweight, durable, corrosion resistant option that meets those safety
demands.
Why use custom aluminum rather than other materials?
Extruded aluminum has a low cost of manufacture compared with other materials
Aluminum and its associated fixings are safer by design
It could be anodized or powder coated maintaining its appearance and won't rust or rot
Aluminum is lighter making it easier to maintain the lighting unit
Xinx ALUM One Stop Manufacturer
We have partnered with many clients to provide tailored solutions to their requirement for custom aluminum in the lighting sector. Our capability to offer a one stop shop solution that includes precise cutting, cnc machining, anodizing,
painting, stockholding of not only the custom aluminum extrusions but also all other parts of the lighting BOM and final assembly, packing and delivery to site. Thus they provide a unique service for their customer base.
Their experience in this sector, aligned with the abilities and equipments they have in-house, make us the ideal partner for all your needs in the lighting industry.
Contact us today if you have any needs for custom aluminum used in lighting market.
|